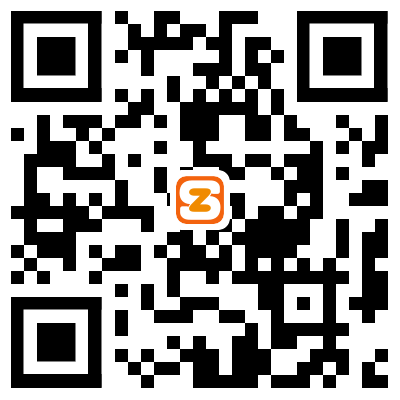

中山市凱恩利機械設備有限公司
主營產品: 車床
大型車銑復合機定制-高剛性車銑復合機-凱恩利
價格
訂貨量(件)
¥110000.00
≥1
店鋪主推品 熱銷潛力款
憩憭憪憬憪憨憦憧憧憬憦





數控車床螺紋切削的三種編程加工方法
C NC車床螺紋切削的三種編程加工方法
前的數控車床中,螺紋切削一般有三種加工方法:G32直進式切削方法、G92直進式切削方法和G76斜進式切削方法,由于切削方法的不同,編程方法不同,造成加工誤差也不同。在操作使用上要仔細分析,爭取加工出精度高的零件。
1、G32直進式切削方法,由于兩側刃同時工作,切削力較大,而且排削困難,因此在切削時,兩切削刃容易磨損。如果我國金屬切削機床能提高技術水平,更好的適應市場需求,相信在未來的發展會越來越好。在切削螺距較大的螺紋時,由于切削深度較大,刀刃磨損較快,從而造成螺紋中徑產生誤差;但是其加工的牙形精度較高,因此一般多用于小螺距螺紋加工。由于其刀具移動切削均靠編程來完成,所以加工程序較長;由于刀刃容易磨損,因此加工中要做到勤測量。
2、G92直進式切削方法簡化了編程,較G32指令提高了效率。
3、G76斜進式切削方法,由于為單側刃加工,加工刀刃容易損傷和磨損,使加工的螺紋面不直的,刀尖角發生變化,而造成牙形精度較差。但由于其為單側刃工作,刀具負載較小,排屑容易,并且切削深度為遞減式。因此,此加工方法一般適用于大螺距螺紋加工。由于此加工方法排屑容易,刀刃加工工況較好,在螺紋精度要求不高的情況下,此加工方法更為方便。在加工較高精度螺紋時,可采用兩刀加工完成,既先用G76加工方法進行粗車,然后用G32加工方法精車。但要注意刀具起始點要準確,不然容易亂扣,造成零件報廢。
4、螺紋加工完成后可以通過觀察螺紋牙型判斷螺紋質量及時采取措施,當螺紋牙頂未尖時,增加刀的切入量反而會使螺紋大徑增大,增大量視材料塑性而定,當牙頂已被削尖時增加刀的切入量則大徑成比例減小,根據這一特點要正確對待螺紋的切入量,防止報廢。智能化是集信息技術、系統控制技術、電子技術、光電子技術、通信技術、傳感技術、軟件技術和專家系統等為一體,實現擴展或替代腦力勞動為目的的高層次的控制技術,是實現數字化工廠的重要技術基礎。數控車床螺紋切削的三種編程加工方法數控車床螺紋切削的三種編程加工方法
直線電機驅動加工中心直線三軸的優缺點
直線電機驅動加工中心直線三軸的優缺點
其實,直線電機的出現讓伺服電機+滾動絲杠驅動裝置很尷尬,因為直線電機可直線代替伺服電機+滾動絲杠來驅動直線三軸。直線電機一般都使用在高速加工中心上,一般數控機床很少采用直線電機驅動直線三軸,因為現在的直線電機驅動三軸技術還夠成熟。
接下來讓小編介紹一下直線電機驅動直線三軸的優缺點吧。
直線電機驅動加工中心直線三軸的優點
直線電機驅動直線三軸有速度快、效率高、剛性佳等優點。東莞數控車床加工,若調換電機后仍不能正常工作,則說明其克制部分不正常,可重點檢查驅動板上的大功率三極管極其保護元件釋放二極管,一般情況下,這兩個元件損壞的幾率比較大。直線電機驅動直線三軸的速度比伺服電機+滾動絲杠驅動直線三軸的速度快2-3倍,伺服電機+滾動絲杠驅動直線三軸的給進速度一般在48m/min,而直線電機驅動直線三軸的給進速度在86m/min;由于伺服電機+滾動絲杠是傳動形式,所以剛性沒有直線電機好。
直線電機驅動加工中心直線三軸的缺點
由于目前直線電機驅動直線三軸的技術不太成熟,所以直線電機還是存在著很多缺點的,比如價格昂貴、發熱量大、傳動平穩性差等缺點的存在。《關于加快振興裝備制造業的若干意見》也提出了中國今后要重點發展的16個重大技術裝備領域。直線電機的制造成本非常昂貴,所以售價也昂貴。由于直線電機速度快,在高速移動過程中會產生一定的熱量,直線電機的速度越快產生的熱量就越高,所以直線電機驅動直線軸裝置必須配備冷卻系統。
cnc加工順序的安排
cnc加工順序的安排
在選cnc加工方法、劃分工序后,工藝路線擬定的主要內容就是合理安排這些加工方法和加工工序的順序。防護裝置:數控車床采用封閉防護裝置可防止切屑或切削液飛出,給操作者帶來意外傷害。零件的cnc加工工序通常包括切削加工工序、熱處理工序和輔助工序(包括表面處理、清洗和檢驗等)。這些工序的順序直接影響到零件的加工質量、生產效率和加工成本。因此,在設計cnc加工工藝路線時,應合理安排好切削加工、熱處理和輔助工序的順序,并解決好工序間的銜接問題。
cnc加工工序的安排:
(1)先粗后精
例如,按照粗車-半精車-精車的順序進行,逐步提高加工精度。鋁材氧化確乎對機械零件精度有影響,因為氧化是一種化學處理方式,會使鋁材外表改性,讓機械零件外表提高硬度的作用。粗車將在較短的時間內將工件表面上的大部分加工余量(如圖2-4所示的爽點畫線內所示部分)切掉。這樣一方面提高了金屬切除率,另一方面滿足了精車的余量均勻性要求。若粗車后所留余量的均勻性滿足不了精加工的要求時,則要安排半精車,以此為精車作準備。精車要保證加工精度,按圖樣尺寸一刀切出零件輪廓。
(2)先近后遠
在一般情況下,離對刀點近代部位先加工,離對刀點元的部位后加工,以便縮短這刀具移動距離,減少空行程時間。對于車削而言,先近后遠海有利于保持坯件或半成品的剛度,改善其切削條件。
(3)內外交叉原則
對既有內表面(內型腔)又有外表面需要加工的零件,安排加工順序時,應先進行內外表面粗加工,后進行內外表面精加工。切不可將零件上一部分表面(外表面或內表面)加工完畢后,再加工其他表面(內表面或外表面)。
(4) 基面先行原則
應優先加工用作精基準的表面。這是因為定位基準的表面越準確,裝夾誤差就越小。例如,軸類零件加工時,通常先加工中心孔,再以中心孔為精基準加工外園表面和端面。
(5)先主后次原則
應先加工零件的主要工作表面、裝配基面,從而及早發現毛坯中主要表面可能出現代缺陷。次要表面可穿插進行,放在主要加工表面加工到一定程度后、最終精加工之前進行。
(6)先面后孔原則
箱體、支架類零件的平面輪廓尺寸較大,一般先加工平面,再加工孔和其他尺寸。這樣安排加工順序,一方面用加工過的平面定位,穩定可靠;另一方面,在加工過的平面上加工孔容易,并能提高孔的加工精度,特別是鉆孔時可以時孔的軸線不易偏。
